GRANBYWARE || Beautiful Everyday Dinnerware Made from 100% Recycled Materials

What if we could turn crushed glass, old tiles, factory sludge and other waste destined for landfill into something amazing?
This was the question Granby Workshop asked, and the result was Granbyware - a collection of beautiful everyday dinnerware made from 100% recycled materials. The forms are simple, strong, and durable - based on hundreds of hand-thrown prototypes they made to test materials and to develop and refine recipes. Every piece from this 100% recycled ceramic tableware collection is handmade in Liverpool and is 100% food, dishwasher and microwave safe.
Beautiful details made possible with the use of recycled materials in the tableware design
“The typical ceramics supply chain is all about refining materials within an inch of their life, removing any impurities and making something smooth and uniform, which is then decorated in a controlled way. Not us though! This supply chain is the opposite.”
THE MATERIALS
The first step in the team’s process was to research the organic chemistry of ceramics and figure out what sources of waste they could up-cycle from nearby areas. They analyzed the core chemical components of our usual clay and glaze materials, and where we could find substitutes from industrial and consumer waste.
They were surrounded by all manner of industries in the North West and only an hour or so from Stoke on Trent - the center of the UK's ceramics industry. The team worked closely with specialist waste management companies to identify a range of waste streams that could be harnessed for producing ceramics.
Simple, strong forms designed for everyday use
They considered all manner of sludges, silts, dust, and debris - everything from incinerated sewage waste ash to recycled car battery compounds. They have been crushing glass, extracting rust, sieving grit, and exploring the extraordinary unseen processes that go on behind the scenes in the wonderful world of waste management.
It’s a serious matter - in the UK, millions of tonnes of ceramic, glass, and stone waste goes to landfill each year. Each year more is recycled - but the reality is that this is really downcycled – where beautiful but broken tiles end up in backfill beneath a road, not a new tile.
That's why Granby Workshop set out to develop their recipe entirely from waste and nothing else - not a single gram of new material, no binders, no additives, strictly waste. Sourced as locally as possible, transformed through their process into a product as beautiful, durable, and long-lasting as anything else out there.
Choose from vibrant blues or more muted hues
THE RECIPE
After countless tests and trials, they developed a process that allows them to make beautiful, durable ceramic dinnerware from a handful of core waste streams.
Industrial clay waste – Before any water is returned to the mains from a factory producing tableware, toilets, or any other ceramic products, it needs to be clean – so all the silty, sludgy, muddy residues are filtered out as waste. These super fine wastewater particles are what binds our clay body together.
Recycled Glass – crushed into a fine powder to form the base of the glaze.
Quarry waste – Dust from slate, granite, and marble quarrying. They add varying amounts of calcium, sodium, iron, and potassium oxide, which in the right quantities control the melt of the glaze.
Recycled refractory bricks – Broken bricks from demolished kilns and furnaces, ground up into a powder. These give us alumina, which helps stiffen and strengthen the glaze, and Magnesia, which helps the glaze melt and gives a beautiful silky matte surface.
Fired ceramic waste – Broken plates, tiles, bricks, bowls, crushed into fine powders. We use them to reduce shrinkage & glaze defects but also to add a splash of colour.
One of the biggest challenges has been accommodating the varied nature of waste. What this means is that each batch is chemically tested using an XRF analysis that shows its mineral composition - then the recipes are tweaked accordingly for that batch. A dash more of tile, a hint of glass, and a sprinkle of quarry waste to perfect the formula.
COLOURS AND FINISH
Not only has this project helped to revamp Granby Workshop’s process to reduce waste and the ceramics industry’s environmental impact, but it has also completely transformed how they see waste materials and helped them explore the beautiful and surprising surfaces, textures and finishes waste can produce.
The typical ceramics supply chain is all about refining materials within an inch of their life, removing any impurities and making something smooth and uniform, which is then decorated in a controlled way. Granby Workshop has taken the opposite approach.
“We’ve got all sorts of speckles and freckles from the impurities. For example our blue isn’t one flat colour – it’s made from tiny specks of crushed blue tiles of varying shade and colour. Oh it’s deep and complex.”
The insides of the pieces have this lovely deep glaze and the exteriors are left raw and unglazed to show off the texture and grain of our recycled clay body. The team worked really hard to develop a clay composition that vitrifies when it’s fired, with water absorption of less than 0.5% so that the outsides can be unglazed and are still completely dishwasher safe.
100% recycled ceramic tableware
We are in awe of the beautiful collection that has resulted from the team’s efforts, and for this project to make an ever-larger impact on the environment and the industry, the team is looking to scale up their efforts via a kickstarter campaign. Visit their website to find out more about Granby Workshop’s latest projects and creations.
Photos courtesy of Granby Workshop
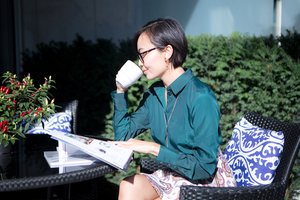